无溶剂复合工艺三大技术风险如何控制?
http://www.packltd.cn 时间:2019年7月2日 关注数:900 次 |
摘要:无溶剂复合工艺显著的优势有降低成本、高效节能、生产安全稳定、提升产品质量等,是一种值得大力倡导、极具实用价值的生产工艺。
无溶剂复合工艺显著的优势有降低成本、高效节能、生产安全稳定、提升产品质量等,是一种值得大力倡导、极具实用价值的生产工艺。
然而,当前无溶剂复合工艺还没有达到成熟阶段,软包装企业在应用过程中仍然存在一些容易被忽视的技术风险,从而导致质量问题的出现。
为此,小编总结了3个较为常见的无溶剂复合技术风险控制要点,并对其原因进行了分析,与行业人士分享。
要点一,无溶剂复合中增加A胶量的技术风险
无溶剂复合双组分(A胶和B胶)胶黏剂混配比例一般是指A胶和B胶的重量比,而不是二者的体积比。
双组分胶黏剂的混配比例一般由胶黏剂生产厂家来确定,因为不同品牌、不同用途胶黏剂的配比一般也不同。
虽然目前国内无溶剂胶黏剂生产厂家有很多,但A胶和B胶重量比的选项并不多,比较常见的A∶B有100∶80、100∶75、100∶50、100∶45等。
但在软包装企业实际的无溶剂复合生产中,双组分胶黏剂的配比会出现失调的情况,这就会对软包装产品无溶剂复合质量产生影响。
案例:
复合结构为OPP/VMPET/PE的软包装袋,经过印刷、无溶剂复合工序后都没有出现质量问题,但在分切制袋后,其封边却出现了卷边现象。
该结构复合软包装袋采用的是某品牌低黏度无溶剂胶黏剂,实际复合生产中A、B胶的配比为100∶67(注意:根据上文所述,与之比较接近的正常配比为100∶75)。
在分析故障原因时,发现袋子卷边的同时还伴随内层胶黏剂不干的现象。原本以为是复合膜熟化程度不完全所致,后延长熟化时间再进行分切制袋,袋子卷边问题依然存在,且开口性也严重变差。
在干式复合工艺中存在“提高固化剂(-NCO组分)可以提高复合强度”的说法,行业人士很容易将这种思路也“复制”到无溶剂复合工艺中,从而导致了较严重的质量事故。
事实上,在无溶剂复合工艺中,无论是-OH过量还是-NCO过量,都可能导致无溶剂胶黏剂不干的现象,只是-OH过量造成的是永久性不干,而-NCO过量造成的是短暂性不干,其还可以与空气中的水分子发生反应而继续固化。
判断二者的简单方法是,将不干的复合层剥离开来,暴露放置在空气中,如果24小时后胶层变干,则说明-NCO组分过量;依然有黏性,则说明-OH组分过量。
通过上述分析,再来判断案例的原因,同时结合A、B胶的配比情况,不难发现袋子卷边主要是由A胶(即-NCO)过量引起的。
由于无溶剂复合膜卷较大,通常延长熟化时间效果并不明显(在这里一定要与熟化温度低的情况区别开来),必须再引入能与-NCO反应的水分来参与交联固化反应。
有人说,在熟化室内放置几桶水来控制熟化室的相对湿度,可达到引入与-NCO反应的水分的效果。
但这样做只对复合膜卷端面及表面的熟化有帮助,对复合膜卷中部的影响很小,因为在熟化环境中,空气中的水分很难渗入复合膜卷中部,反而会使整体熟化效果出现偏差。
比较行之有效的是,将复合膜卷在分切机上进行一次倒卷再进行熟化,同时增加车间环境的湿度(使用加湿器),使得复合膜层间及表面吸附一部分水分,在熟化时这些水分会渗入到胶层与过量的-NCO发生交联固化反应,从而使未干胶层进一步充分固化,进而有效解除软包装袋卷边现象。
要点二,无溶剂复合中PE薄膜剥离强度衰减的风险控制
薄膜吹塑中会添加一定量的爽滑剂,以降低薄膜之间、薄膜与设备之间的摩擦力,使薄膜表面更为光滑,使得复合膜在生产过程以及包装机上运行更为顺畅。
通常情况下,PE薄膜中会适度添加过量爽滑剂,这样能在一定程度上解决无溶剂复合膜熟化后摩擦系数异常增大的现象,但这也会导致复合膜的剥离强度发生衰减。
严重时,在熟化完成时就能检测到复合膜剥离强度不达标,而大部分情况是在复合膜放置过程中或者软包装袋的流通过程中,才出现剥离强度的衰减。
案例1:复合结构为BOPA/PE光膜
主要参数:
某品牌无溶剂胶黏剂,涂胶量为1.5g/m2,40℃温度下熟化24小时。
该复合膜剥离强度的跟踪检测数据如下:
10月13日检测:横向剥离强度为15.37N/m。
11月4日检测:横向剥离强度为4.62N/m,
将复合层剥离开来后,PE薄膜表面有一层用手可擦拭掉的雾状物质,如图1所示。
11月18日检测:横向剥离强度为4.69N/m,
与上次检测数据接近,说明复合膜的剥离强度达到了稳定值。
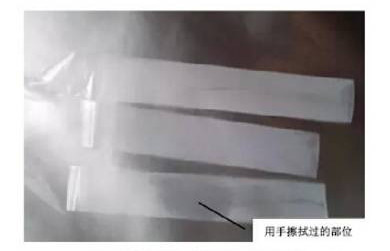
通常,软包装企业只对熟化后不久的复合膜剥离强度进行检测,很少会跟踪测试放置过程中的复合膜或流通过程中的软包装袋的剥离强度是否出现衰减,在此应该引起注意。
案例2:复合结构为消光OPP/PET/抗静电PE
主要参数:
某品牌无溶剂胶黏剂,涂胶量为1.5g/m2,42℃温度下熟化24小时。
同样选择了3个时间点进行剥离强度的跟踪检测,检测结果为:纵向剥离强度分别为2.08N/15mm(PET膜发生断裂)、1.82N/15mm、1.79N/15mm;横向剥离强度分别为2.97N/15mm、2.75N/15mm、2.69N/15mm。
纵向剥离强度衰减严重,横向剥离强度衰减不明显,而且在最后一次检测时同样发现PE薄膜表面有一层可用手擦拭掉的白色物质,用溶剂擦拭表明胶层在PE膜一侧。
从以上2个案例可以看出,无溶剂胶黏剂在PE薄膜中的迁移会将爽滑剂带出,这是导致复合膜剥离强度衰减的主要原因,建议可以使用耐无溶剂胶黏剂迁移的爽滑剂添加配方,这样既可以解决PE薄膜在无溶剂复合中的摩擦系数变化问题,也可以解决剥离强度的衰减问题。
要点三,注意鉴别无溶剂 胶黏剂的气味特征
曾有人问:“结构OPP/VMPET/PE的复合膜,采用无溶剂复合后有残留气味,而采用干式复合却没有,请问是什么原因?”
引起软包装袋产生异味的因素较多,如残留溶剂、油墨树脂、薄膜原料树脂、胶黏剂等,尽管无溶剂复合不存在溶剂残留的工艺风险,但无溶剂胶黏剂中树脂及配方具有一定的气味特征,有些在复合固化后,甚至还有些在包装内容物后仍存在一定影响。
对于软包装企业来说,一定要注意鉴别无溶剂复合后复合膜是否有异味,防患于未然。
关于复合膜异味的检测方法,GB/T 10004-2008《包装用塑料复合膜、袋 干法复合、挤出复合》标准有相关规定。
(1)在GB/T 10004-2008标准中规定了包装感官指标检测方法:打开包装箱及内衬的包装膜,即时闻是否有异嗅。
(2)GB/T 10004-2008的6.6.16.2规定,取10cm×10cm的薄膜一张,裁成条状,放入盛有150ml蒸馏水的器皿中,盖上盖子密封,放入60℃的烘箱或水浴中,30min后取出,打开盖子,闻水蒸气的气味,判断是否有异味。
(3)方法2实际较少使用,通常都是取一定面积的复合膜,剪碎封装入500ml的玻璃瓶,在60~80℃温度下烘烤30min,感官检测是否有异味。
也可以将包装袋封入空气或实际内容物后,在50~60℃温度下旋转数小时,撕开包装,感官检测是否有异味。
复合膜的异味主要来源于无溶剂胶黏剂,所以一般无溶剂胶黏剂的气味特征,可用如下方法鉴别。
(1)取一定量的不同品牌A胶和B胶,进行感官检测对比。
(2)相同结构原材料的复合膜,用不同无溶剂胶黏剂复合后,取样按复合膜异味判断方法2进行鉴别。
(3)将按说明书比例混配好的无溶剂胶黏剂加入玻璃瓶中(瓶底垫张塑料单片膜,胶黏剂固化后方便取出),于40~50℃交联反应24~48小时后,鉴别其气味特征。
该方法比较贴合实际应用,其包括树脂本身的气味特征、未反应完全的低分子量成分可能产生的气味特征,交联固化时可能存在的副反应产物的气味特征。
(来自:包装企业网)